Devido às suas características de alto desempenho e baixo custo, o aço galvanizado é universalmente usado para a colocação de tubulações e a criação de estruturas para diversos fins. A maneira tradicional de unir produtos de metal é a soldagem de tubos galvanizados. Esse processo possui vários recursos que devem ser levados em consideração.
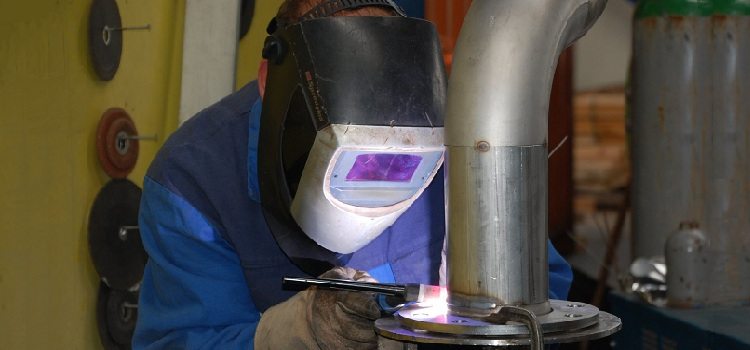
A soldagem de tubos galvanizados é um processo simples, mas você precisa conhecer os meandros de trabalhar com esse material
Conteúdo
É possível soldar tubos galvanizados? Métodos de soldagem
Com a ligação térmica, a superfície do metal no local da costura é exposta a uma temperatura de cerca de 1200 graus, enquanto o zinco ferve a 906 graus Celsius. Portanto, durante o processo de soldagem, o revestimento de zinco queima. Os seguintes fenômenos negativos estão associados a este aspecto:
- O zinco em estado gasoso é muito prejudicial à saúde. Sem ventilação de alto desempenho, a probabilidade de envenenamento do soldador e asfixia temporária é alta.
- Na solda, o revestimento de zinco é quebrado e a proteção contra corrosão é perdida.
- A evaporação intensiva de zinco durante a soldagem contribui para o aparecimento de poros e rachaduras de inter-cristalização. O composto resultante não será confiável devido à sua baixa resistência.
Dado o exposto, o soldador deve necessariamente observar o aumento das medidas de segurança. Durante o cozimento, um respirador especial e uma máscara protetora feita de materiais dielétricos são colocados no rosto. A proteção das mãos é fornecida por luvas de borracha revestidas com um pano isolante térmico. Para evitar a formação de espuma desnecessária na camada de zinco, permite o processamento da superfície articular com ácido clorídrico. Para um resultado de alta qualidade, é imperativo evitar a evaporação da camada de zinco. Essa condição pode ser fornecida por várias opções de soldagem.
A primeira maneira é limpar mecanicamente a zona de solda de zinco com uma roda de esmeril abrasiva ou escovar o metal. Nesse caso, o galvanizado é soldado como tubos pretos comuns. O ponto negativo é que a costura sem zinco é desprovida de proteção contra corrosão, e isso afeta negativamente a vida útil do produto. Como resultado da umidade, o tubo enferruja rapidamente e a área afetada precisará ser substituída. Isso significa que, no futuro, haverá custos adicionais em dinheiro e custos de tempo para a alteração da estrutura.
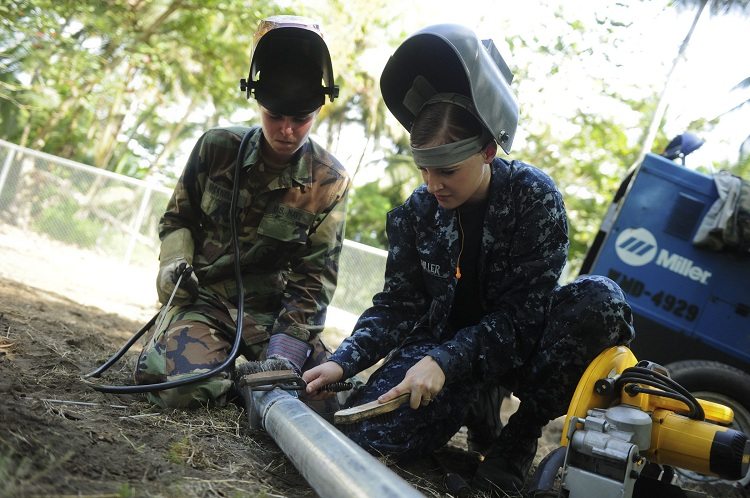
Limpar a área de solda antes de iniciar o trabalho impedirá a evaporação do zinco da superfície do tubo
Nota! Uma pequena área superficial sem uma camada anticorrosiva pode ser protegida pelo caminho do cátodo (o zinco é transferido para a zona exposta pelo método eletroquímico).
É possível obter juntas soldadas de alta qualidade sem danificar o revestimento anticorrosivo aplicando fluxos especiais ao soldar. Esta tecnologia é aplicável nos casos em que a limpeza de juntas de zinco é tecnologicamente impossível. Ao conectar, são utilizados o fluxo HLS-B e a liga UTP 1. O método é ideal para cozinhar utilidades no abastecimento de água. O fluxo não é prejudicial à saúde, porque se dissolve completamente no ambiente aquático sem a formação de compostos nocivos.
Como cozinhar tubos galvanizados usando fluxo
As bordas dos tubos antes da conexão são desengorduradas e limpas para um estado de brilho metálico. A limpeza deve ser realizada não apenas por fora, mas também por dentro. As pré-formas são pré-aquecidas de 20 a 30 cm de comprimento em cada lado da junta planejada. Para soldagem eficiente de produtos com espessuras de parede de até 3 mm, não há necessidade de preparação específica de arestas. A largura do espaço entre as extremidades é igual a 2-3 mm. Com tubos mais espessos, são executados um ângulo de abertura de 80 a 90 graus e uma altura de embotamento de 1 a 1,5 mm. A largura do espaço é semelhante.
O fluxo é aquecido a um meio entre líquido e sólido e é aplicado em uma camada espessa à superfície do composto. A quantidade de material usado é duas vezes maior do que na soldagem de produtos de aço comuns. O objetivo do fluxo é retirar o excesso de calor da máquina de solda, o que impede a evaporação do zinco pelas bordas.
Quando aquecido, o fluxo muda de cor de amarelo para branco e, quando a junta atinge a temperatura de solda, se transforma em transparente. Assim, o estado do fluxo pode determinar o tempo para começar a soldar.
Selecionando o tamanho do bico do queimador para solda, você precisa começar pela espessura da parede do produto galvanizado. A proporção do tamanho é mostrada na tabela nº 1.
tabela 1
Tamanho do bico mm | Tubo galvanizado |
1 -2 | diâmetro até 250 mm, espessura de parede 2-6 mm. Preenchimento de costuras em produtos de qualquer tipo |
2-4 | diâmetro superior a 250 mm e espessura superior a 2-6 mm |
Na soldagem por galvanização, a regra se aplica: o bico do queimador deve ter um tamanho menor do que quando se une a um tubo de aço convencional de dimensões semelhantes.
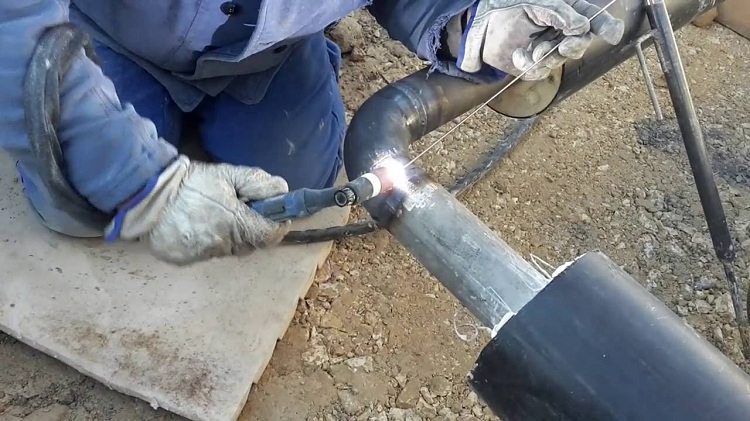
Para soldagem de alta qualidade de um tubo galvanizado, é extremamente importante escolher uma tocha do tamanho apropriado e ajustar corretamente a chama
Por que é importante escolher o bico certo? O uso de uma versão grande demais superaquecerá a peça de trabalho e o zinco evaporará. Isso significa que suas características de resistência à corrosão e resistência se deteriorarão (o zinco fundido levará à formação de poros). Se o bico não for grande o suficiente, a superfície do metal não esquentará até a temperatura necessária, o que fará com que a solda adira a ele.
Durante a solda, é utilizada uma chama de acetileno-oxigênio, que é exposta ao excesso de oxigênio. Um excesso de oxigênio é necessário para que, quando a solda derreta, seu óxido seja formado como resultado da reação com o silício. É o óxido de silício que evita a evaporação térmica do zinco.
Importante! É necessário ajustar e garantir a estabilidade da chama do queimador. O calor deve ser focado nas bordas e no espaço entre as peças. Chama instável leva ao superaquecimento da seção do tubo perto da conexão.
Para soldar com uma tocha de gás, é melhor usar a técnica "esquerda", ou seja, colocar a barra na frente da chama. Nesse caso, o fogo cairá na barra de solda e não na superfície do metal. Ao realizar uma costura de refusão, o queimador deve ser inclinado em um ângulo de 70-75º. Para a passagem de preenchimento, o ângulo deve ser de 15 a 30º. A tocha pode ser posicionada em qualquer posição espacial, mas a mais conveniente é a mais baixa; é conveniente monitorar a piscina de solda com ela. A união de tubos com até 4 mm de espessura ocorre em uma passagem. Se o valor da espessura for maior, será usada a soldagem de várias passagens.
Após a conexão, a junta soldada é limpa do excesso de material de solda. Lá fora, o tubo é lavado com água e mantido com uma escova de arame. É importante não exagerar, para não danificar a superfície do zinco. A concha interna deve estar cheia de água por um dia e enxaguada.
A soldagem adequadamente executada de tubos galvanizados permite obter costuras de conexão que não exigem proteção adicional contra corrosão.
Soldagem a arco manual de tubos galvanizados
Reduzir a velocidade de soldagem e aumentar a corrente evita a formação de poros nas soldas de filete e de topo.O uso de eletrodos especializados pode fornecer tais condições. É especialmente importante fazer a escolha certa de como cozinhar um tubo galvanizado, dependendo do tipo de aço. Ao conectar peças de carbono galvanizadas por soldagem a arco manual, é necessário parar nos eletrodos revestidos com rutilo. Para aços de baixa liga, eletrodos revestidos básicos podem ser usados. Os eletrodos de rutilo têm várias vantagens:
- O eletrodo contém óxido de titânio, que permite inflamar o arco de maneira rápida e fácil, pela primeira vez e repetidamente.
- O arco de soldagem resultante fornece soldas apertadas de alta qualidade, sem rachaduras, com alta resistência à fadiga.
- A perda de material fundido devido a respingos é mínima.
O revestimento rutílico do eletrodo pode conter algum pó de ferro. Isso permite reduzir a gravidade específica do carbono na camada de zinco e aumentar a resistência ao cracking.
A soldagem elétrica de tubos de perfil galvanizado requer pelo menos uma experiência mínima com o soldador. Além de revestir o eletrodo, sua espessura é de grande importância. A potência do arco depende diretamente do tamanho do eletrodo. A escolha de um eletrodo muito espesso pode levar à queima e características de força muito finas a fracas do composto. A espessura da parede mais comum dos produtos de perfil é de 1,5 a 5 mm, portanto, você deve escolher um eletrodo com um diâmetro de 2 ou 3 mm.
No processo de soldagem, a velocidade de movimento do eletrodo através do metal é de particular importância. Em um ritmo lento, existe o risco de queimar o tubo, um ritmo muito rápido não fornecerá a qualidade necessária da costura de conexão. A velocidade adequada é desenvolvida durante o treinamento.
Nota! Após a soldagem, a junta e a zona afetada pelo calor devem ser tratadas com um composto anticorrosivo.
O agente de proteção deve ter as seguintes qualidades:
- alta adesão à superfície do metal;
- resistência à corrosão ao nível de zinco;
- facilidade de aplicação sem equipamento caro de alta tecnologia.
Como camada protetora, a tinta, que inclui pelo menos 94% de pó de zinco, funcionou bem. Aglutinantes sintéticos insaponificáveis são utilizados para a sua fabricação, portanto são mantidos em superfícies verticais e fáceis de aplicar.
Outra maneira de restaurar a superfície é aplainar 99,99% de fio de zinco contendo 99,99% de zinco. As hastes de zinco-cádmio também são adequadas para esse papel.
Métodos alternativos de união de tubos galvanizados
A galvanização térmica sem zinco pode ser unida por rosqueamento. Devido à complexidade da aplicação, é utilizado apenas em tubos de pequeno diâmetro. O ponto negativo dessa conexão é o alto custo do trabalho em comparação com a soldagem tradicional. Também é importante notar que na junção durante o processo de corte, a camada de zinco será danificada. Consequentemente, o tubo na junção será mais suscetível à corrosão.
No fornecimento de água, fornecimento de calor e outras redes de engenharia, podem ser utilizados sistemas soldados na fábrica, montados de acordo com o princípio do projetista. Um kit fabricado na fábrica inclui uma luva com uma vedação que aparafusa a uma ranhura nas bordas do tubo. Esse método é bastante novo para os países da CEI; suas principais vantagens são a alta velocidade de instalação e conexões confiáveis.
Concluindo, notamos que, com uma junta soldada, são possíveis costuras de alta qualidade com estrita observância de todas as regras. Antes de tudo, o superaquecimento e a evaporação do zinco devem ser evitados, o que é possível apenas com o uso de eletrodos e fluxo rutílicos especiais. As qualificações do soldador desempenham um papel importante na soldagem a arco elétrico e a gás. Outros métodos de tubos não são tão populares devido ao menor custo de soldagem.